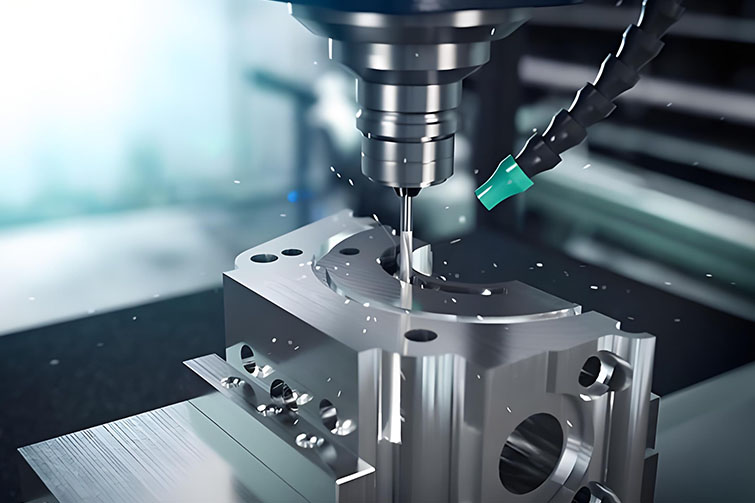
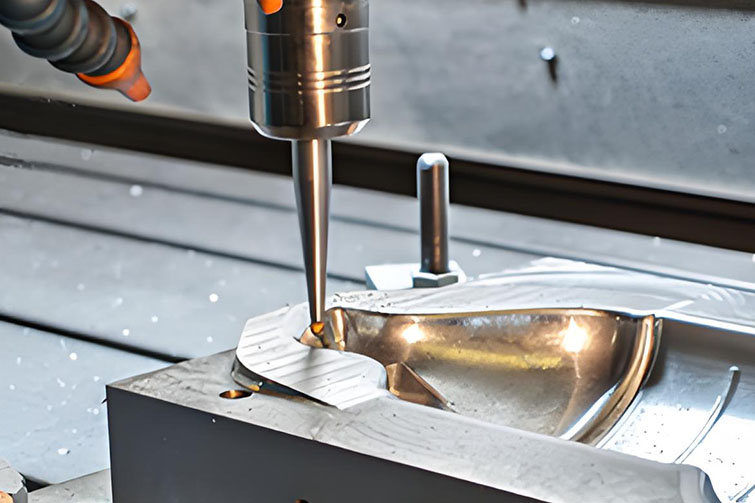
Cam Precision Machining Services: Ensuring Perfect Motion Control
In industries that rely on precise motion control, such as automotive, robotics, and manufacturing equipment, cam precision machining is a critical service. The cam is a mechanical component that converts rotary motion into linear motion, and its precise manufacture is essential to ensuring smooth, efficient, and reliable operation.
What is Cam Precision Machining?
Cam precision machining refers to the manufacturing process of cam components, which are used in various machines to convert rotational motion into linear motion. The cam system consists of a camshaft (the rotating part) and cam followers (the parts that follow the cam's motion). These components are typically used in engines, automated systems, and other mechanical applications requiring precise movement.
The precision of the cam is crucial as even a minor error in its geometry or dimensions can lead to malfunction, decreased performance, or complete failure of the system. CNC (Computer Numerical Control) machining is commonly employed for cam manufacturing due to its ability to achieve high accuracy and consistency.
Key Features of Cam Precision Machining
- High-Precision Geometry: Cams come in a variety of shapes and profiles (e.g., radial, axial, or cylindrical) depending on their function. Precision machining ensures that the cam’s profile is accurate, so the cam follower moves in the desired manner. The level of precision can be as tight as 0.001mm, ensuring smooth motion transfer.
- Complex Designs: Some cams are highly complex, with varying profiles and multiple interacting parts. CNC machining allows for the creation of intricate, multi-profile cams that would be difficult or impossible to achieve through traditional methods. These cams are vital for high-performance machinery.
- Durability and Material Selection: Cams are often made from hard materials such as hardened steel, stainless steel, or even specialized alloys, depending on the application. Precision machining ensures that these materials are processed without compromising their inherent strength and durability.
- Surface Finish: The surface quality of cam components is crucial because it directly impacts the efficiency of the motion transfer. CNC cam machining often includes post-machining processes like grinding or polishing to achieve a smooth, wear-resistant surface.
Applications of Cam Precision Machining
- Automotive Industry: In internal combustion engines, cams control the opening and closing of valves, influencing engine performance. The precision of these camshafts is essential for optimal engine efficiency, power, and fuel economy. CNC precision machining allows for the mass production of highly accurate camshafts for cars, trucks, and motorcycles.
- Industrial Machinery: Many industrial machines use cams to control processes such as material handling, packaging, or assembly. CNC machining ensures that the cams used in these machines are designed and produced to meet strict performance standards, ensuring smooth and reliable operation.
- Robotics: In robotic arms and automation equipment, cams help convert rotary motion into linear movement, enabling precise control of tool heads, grippers, and other components. Precision machining ensures that these cams are capable of delivering the high repeatability and accuracy required in robotics.
- Aerospace: Cam precision machining is used in the aerospace industry for various applications, including control systems, landing gear, and throttle mechanisms. The safety-critical nature of these applications demands that cam components be manufactured to exacting standards.
- Medical Devices: Cams are also used in medical equipment such as infusion pumps, prosthetics, and surgical robots, where precise motion control is vital. The demand for high-precision, durable, and reliable cam components is met through advanced CNC machining techniques.
Benefits of Using Cam Precision Machining Services
- Improved Motion Control: The primary benefit of precision cam machining is that it ensures accurate motion control. By maintaining tight tolerances and producing custom profiles, the cam performs its intended function without errors, resulting in smoother operation and enhanced system performance.
- Customization: Each machine or system may require different cam profiles. Precision cam machining services can create custom cams that fit specific applications, ensuring that each cam component meets the unique requirements of the machine or device.
- Reduced Wear and Tear: With precision machining, cam components are created with superior surface finishes and material hardness. This not only reduces friction but also extends the lifespan of the cam and the machine it's part of, leading to lower maintenance costs over time.
- High Consistency and Reliability: CNC machining offers high repeatability, meaning that once a cam profile is created, it can be reproduced with exact consistency. This makes it easier for manufacturers to produce high-volume, uniform cam components for large-scale production runs.
- Cost-Effective for Mass Production: Though the initial design and setup costs may be high, CNC cam machining allows for efficient mass production with minimal material waste, making it a cost-effective solution for producing large quantities of cam components.
Conclusion
Cam precision machining plays a pivotal role in industries that rely on precise motion control. Whether it’s for automotive, aerospace, robotics, or medical devices, the need for accurate and reliable cam components cannot be overstated. Thanks to CNC machining technology, manufacturers can produce high-precision cams with custom profiles, durability, and smooth motion transfer, ensuring that every system operates at peak performance.
By utilizing cam precision machining services, businesses can not only enhance the functionality and efficiency of their machines but also reduce operational costs, improve reliability, and meet the increasingly stringent demands of modern industries.